Powder Coating Troubleshooting Guide
Chapter Ten: Powder Application Tips
Alleviating the Faraday Cage
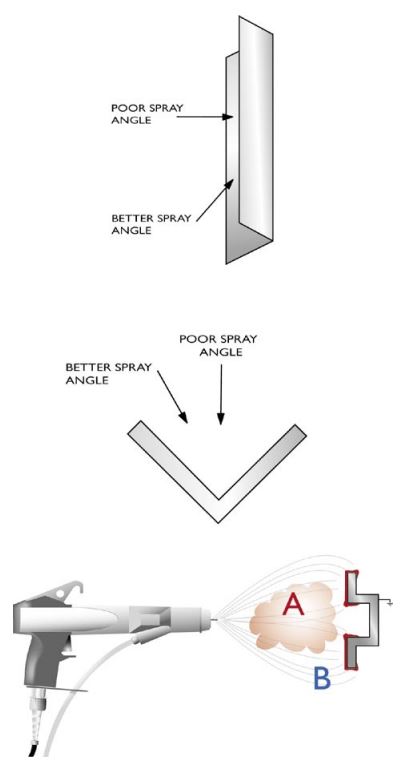
Overcoming the Obstacles of the Electrostatic Process:
- Blast powder into the recesses
- Increase the powder flow rate
- Maximize the gun to part distance
- Use slotted tip to concentrate the spray
Using the Electrostatic Process:
- Finesse the powder into recesses
- Decrease powder gun flow rates
- Reduce the gun’s microamps (µA) to 20
- Maintain gun to part distance of ~ 8-10"
- Use slotted tip to concentrate spray
- Approach recess at an obtuse angle
Spraying in the Faraday Cage:
Spraying at the recesses of a part at an obtuse angle can help to apply the coating properly.
- It reduces air turbulence
- Allows deeper penetration
- Minimizes early back ionization
- Utilizes more lines of force
A: Lines of Force
The corona generated charge field and lines of force tend to create Faraday cage difficulties.
B: Particle Space Charge
Lowering the voltage and allowing space charge created by powder cloud to develop near the recess will help with penetration.
Impact Fusion
Impact fusion occurs when powder is subjected to high velocity and/or a restriction in its path. This creates excess friction, softening and depositing of powder at the point of contact.
Impact Fusion on Hoses
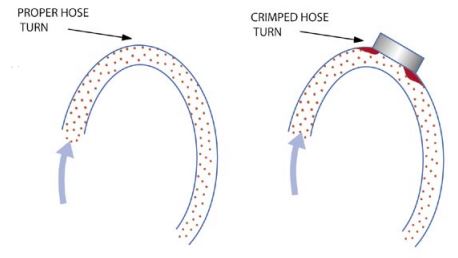
Causes of Impact Fusion:
- Plugged or worn pump sleeves
- Scratched or burred venturis
- Crimped, worn, or cracked hoses
- Deflectors and gun nozzles
- Powder pathway diameter change
- Heat present on powder pathway
- Excessively high gun pressures
- Low glass transition temperature powder
- Powder particle size to fine
- Moisture in the air supply
Venturi Impact Fusion
Venturi and Gun Controls
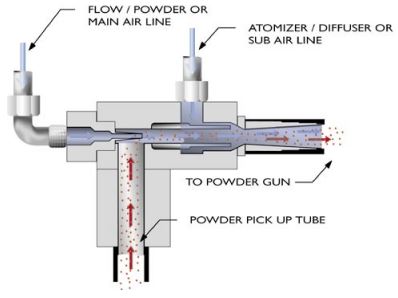
Typically 2-3 Air Controls per Gun:
- Powder Regulator (also called Flow or Main) controls the amount of powder being sprayed and the velocity and throw of the powder.
- Atomizer Regulator (also called diffuser or Sub) controls the density and size of the powder cloud as well as insuring steady output.
- Swirl Regulator (also called TIP) delivers air directly to the gun tip which can shape the cloud and prevent powder build up at the electrode and deflector.
Powder, Flow, or Ejector Rate
Too Low:
|
![]() |
Too High:
|
Atomizer or Diffuser Rate
Too Low:
|
![]() |
Too High:
|
Optimizing Gun Pressures
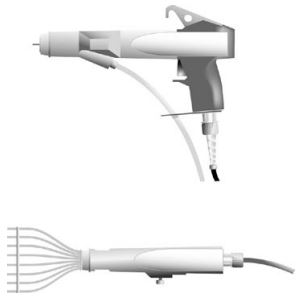
Excessive gun pressures will have a dramatic NEGATIVE impact on spray quality and efficiency.
Too much powder/flow pressure can:- Cause excessive wear of equipment
- Create impact fusion problems
- Cause gun spitting and puffing
- Increase film thickness uniformity
- Decrease first pass transfer efficiency
- Increase amount of reclaim or overspray
- Reduce electrostatic attraction:
- Large particles can bounce off
- Particles traveling too fast for wrap
- Less time in corona field charge
- More particles to share charge
- Increased friction generates high static (positive) charge and reduces the effectiveness of the corona (negative) charge
Factors Affecting Charge
- Composition
- Resin type
- Resin content - (% used in formula)
- Particle size
- Particle shape
- Substrate type - (conductivity)
- Substrate shape - (flat, frame, recess, etc.)
- Substrate size
- Substrate temperature
- Line speed - (time to spray)
- Booth air flow
- Humidity
- Gun to particle distance
- Virgin to reclaim ratio
- Quality of ground
- Gun flow rates - (volume and speed)
- Gun tips & deflectors
- Gun voltage & current - (amount of charge)
Optimizing Gun Tips
Deflector Size Affects on Powder Cloud:
- Determines peak film build and uniformity
- Determines size and coverage area of cloud
- Concentrates powder along edges of pattern
- Gives more uniform deposit with moving parts
Nozzle Affects on Powder Cloud:
- Develops flat rather than conical spray pattern
- Typically covers much smaller spray area
- Heavier build in center of spray pattern
- Concentrates more powder into recesses
Applying a Second Coat
Many obstacles associated with back-ionization are also encountered with a second coat of powder:
- Cured film is a better dielectric insulator than powder
- Film has no way to bleed off free ions
- First coat gains charge rapidly
There are techniques to help in the application of a second coat:
- Reduce microamps (µA) to 10
- Increase gun to part distance
- Slightly increase cloud density
- Use current limiting gun if possible
- Use free ion collecting device
To ensure good intercoat adhesion, it is also recommended that the coating be lightly sanded and then cleaned.
Other Chapters
- Early Powder Coatings, Uses, and Types
- Manufacturing of Powder Coatings
- Powder Chemistries, Formulations, Comparisons, and Uses
- Comparisons to Liquid Coatings
- Measuring Up the Product
- Pretreatment
- Powder Application Methods and Equipment
- Powder Coating Recovery Equipment
- The Electrostatic Charge Process
- Powder Curing Process
- Safety Issues With Powder Coatings
- TCI Troubleshooting Guide
- Glossary of Industry Related Terms